Over the years, manufacturing industries have undergone transformations driven by technological advancements and globalization. They have adopted this advancement to stay relevant and competitive in the evolving global market. These adoptions are driving efficiency, flexibility, and innovation, shaping the future of manufacturing.
With remote work becoming the norm, manual expense management processes that relied on physical receipts and paperwork became significantly more challenging.
As factories strive to stay ahead, leveraging automated expense management helps to facilitate financial processes. It also empowers companies to make data-driven decisions, enhance cost control, and foster sustainable development.
To help you, we've co-authored this blog with Melissa Terry, CFA at VEM Tooling, a plastic manufacturing solution. From her 10+ years of experience, she’s helped us flesh out this guide, where we’ll analyze strategies, tools, and best practices to revolutionize how manufacturing businesses approach their expenses.
So, let's get started!
Types of Manufacturing Expenses
In every manufacturing company, there are costs incurred during product production. These expenses include;
- Direct material costs: These are the raw materials used directly in manufacturing the final product. For example, direct materials with medical product processes include; plastics, metals, and electronic components. It also includes the consumables used in the production process, such as lubricants, cleaning supplies, and packaging materials.
- Direct labor: This encompasses work that can be traced to individual units produced. It is that portion of the labor cost of the production process assigned to a production team. Thus, all the workers who have a hand in refining, assembling, and manufacturing your products are included here.
- Manufacturing overhead: All costs that are not direct labor or materials are overhead. These are costs that apply to units of production based on a variety of allocation systems. They include direct labor hours and machine hours incurred. It also includes all the indirect materials and labor costs with a secondary or support role. An example includes; the cost of utilities, rent, and insurance.
These expenses are presented in the income statement as separate line items. It can be thrilling and exciting to have a manufacturing business. However, managing and earning enough profits can be challenging as there are numerous expenses to deal with.
What Is Manufacturing Expense Management, and Why Is It Important?
Manufacturing expense management is the process of tracking, controlling, and optimizing the costs associated with manufacturing a product. It involves identifying all the costs involved in manufacturing, tracking them over time, and making required adjustments to keep costs in line with the budget.
Manufacturing expense management is essential for several reasons:
- It can help manufacturers to identify cost-saving areas
- It can enable manufacturers to make better pricing decisions
- It can aid manufacturers to improve their profitability
Manufacturer expense management is an important part of running a successful manufacturing business. Manufacturers can improve their profitability and stay competitive by carefully tracking and managing their expenses.
Challenges with Manual Manufacturing Expense Management
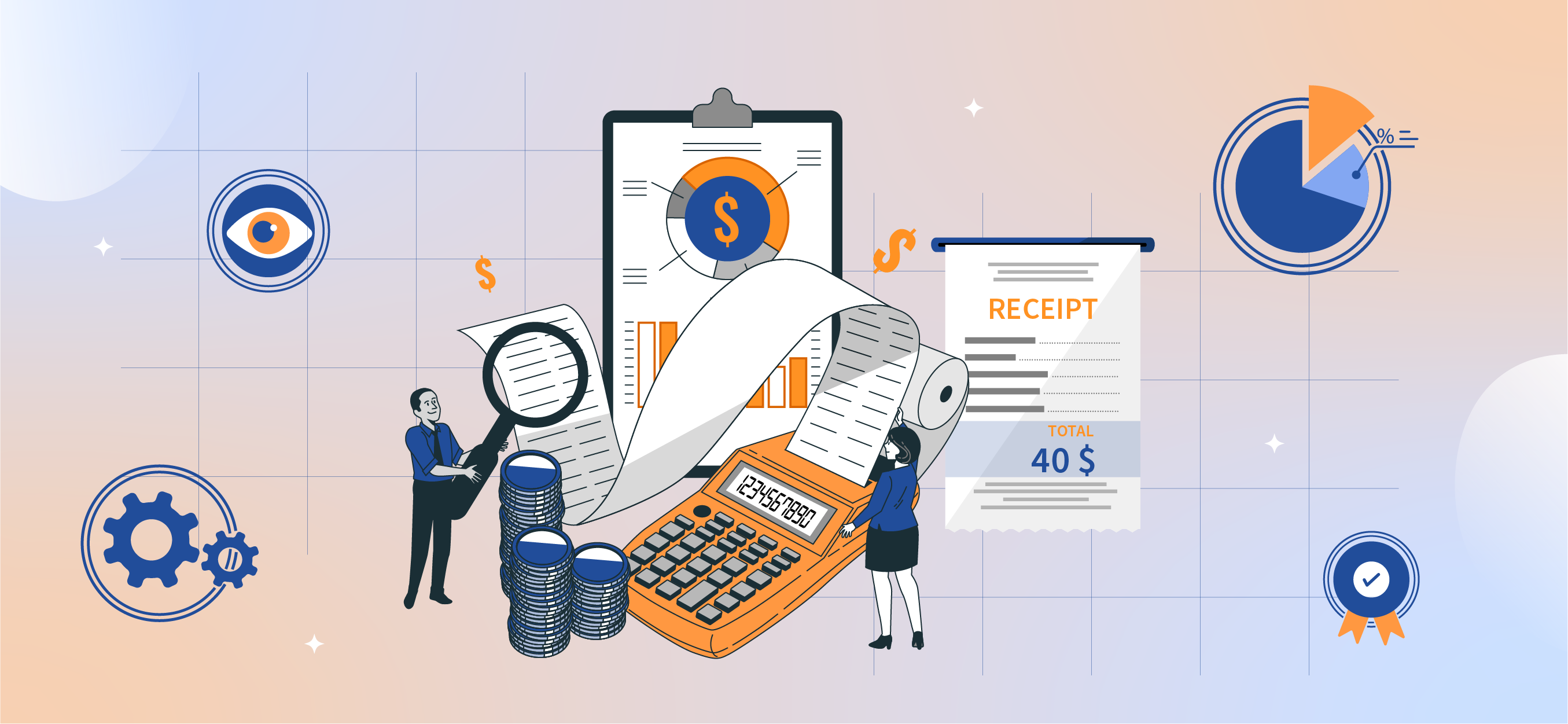
While manufacturing expense management streamlines operations, when done manually, it comes with its challenges. The process depends heavily on valid and reliable data. However, compiling and maintaining updated data across different systems and departments takes a lot of work.
Based on experience, Mellisa recounts her challenges with traditional manufacturing expense management at VEM Medicals.
1. Data collection
Compiling and gathering expense data manually is very time-consuming. At VEM Medicals, we work with diverse suppliers, ranging from raw material providers to component manufacturers. Each supplier has different billing systems and invoicing processes. They also have different data formats, making merging financial information difficult. It is also tedious when this data is collected manually, leading to mistakes and errors.
2. Data entry and processing
Once the data is compiled, it must be manually entered into spreadsheets and accounting systems. We deal with data like; product specifications, batch numbers, quality test results, and compliance documentation. Manually entering all this information can be a laborious process highly prone to human error. These human errors include data entry mistakes or transposition errors. This would always lead to inaccuracies and mistakes in expense records.
3. Inefficient workflows
Managing manufacturing expenses manually involves a complex workflow. This workflow requires multiple approvals, monitoring, and reconciliations. At VEM Medicals, we lacked real-time tracking mechanisms for expenses. As a result, monitoring and tracking expenses throughout the manufacturing process became challenging. This inefficiency made it difficult to identify cost overruns, excessive spending, or potential areas for cost savings. We mainly attribute the problem to workflows that depend on manual communication methods like emails and paper-based processes.
4. Lack of visibility
When managing manufacturing expenses manually, monitoring them in real time becomes cumbersome. Manual expense management processes do not have real-time visibility into company expenses. It isn't easy to analyze spending patterns to make good decisions. Lack of visibility also hinders identifying potential cost-saving opportunities.
5. Compliance and audit risks
Manual processes are more open to compliance errors. These errors include non-compliant expense claims and a need for supporting documentation. At VEM Medicals, expenses related to regulatory compliance, such as conducting clinical trials, getting necessary certifications, or implementing quality control measures, must be properly documented and justified. Failure to comply with these regulations results in fines, product recalls, or legal repercussions.
6. Time and resource intensive
Developing a new medical device involves research and development (R&D) efforts. This includes conducting market research via market research tools, analyzing existing technologies, designing prototypes, and testing them for safety and efficacy.
Managing the manufacturing expenses of these activities manually requires a lot of commitment, time, and effort from workers. As a result, it diverts resources from more strategic and vital tasks. This impacts overall productivity and efficiency.
7. Limited scalability
As manufacturing operations thrive, the amount of work increases, and so does the finances. As the finances increase, manual processes become significantly challenging to scale. Handling significant expenses, extra suppliers, and expanding teams can overwhelm manual systems. This leads to delays and inefficiencies.
8. Lack of integration
Managing manufacturing expenses manually involves operating in isolation from other business systems. Without integrations, accessing accurate and up-to-date financial data also becomes a challenge.
For instance, when our finance department needed real-time visibility into procurement activities, we faced difficulties tracking expenses and negotiating better contracts with suppliers. This was because of the lack of integrations that led to disorganized processes, data duplication, and increased chances of errors.
10 Reasons Why Manufacturing Companies Need an Automated Expense Reporting Solution
Expense management for manufacturing, when implemented efficiently, has perks and advantages. These benefits significantly impact the overall performance and profitability of a manufacturing organization. They include:
1. Streamlined expense tracking
Manufacturing companies handle plenty of expenses. These expenses include raw materials, equipment maintenance, travel, and employee payment. An automated expense management automatically captures and categorizes expenses, reducing the manual effort required.
It also enables manufacturers to track expenses in real-time. This includes capturing data on purchases, invoices, receipts, and other financial transactions related to manufacturing operations. By automating the tracking process, organizations can reduce manual errors, improve accuracy, and gain better visibility into their expenses.
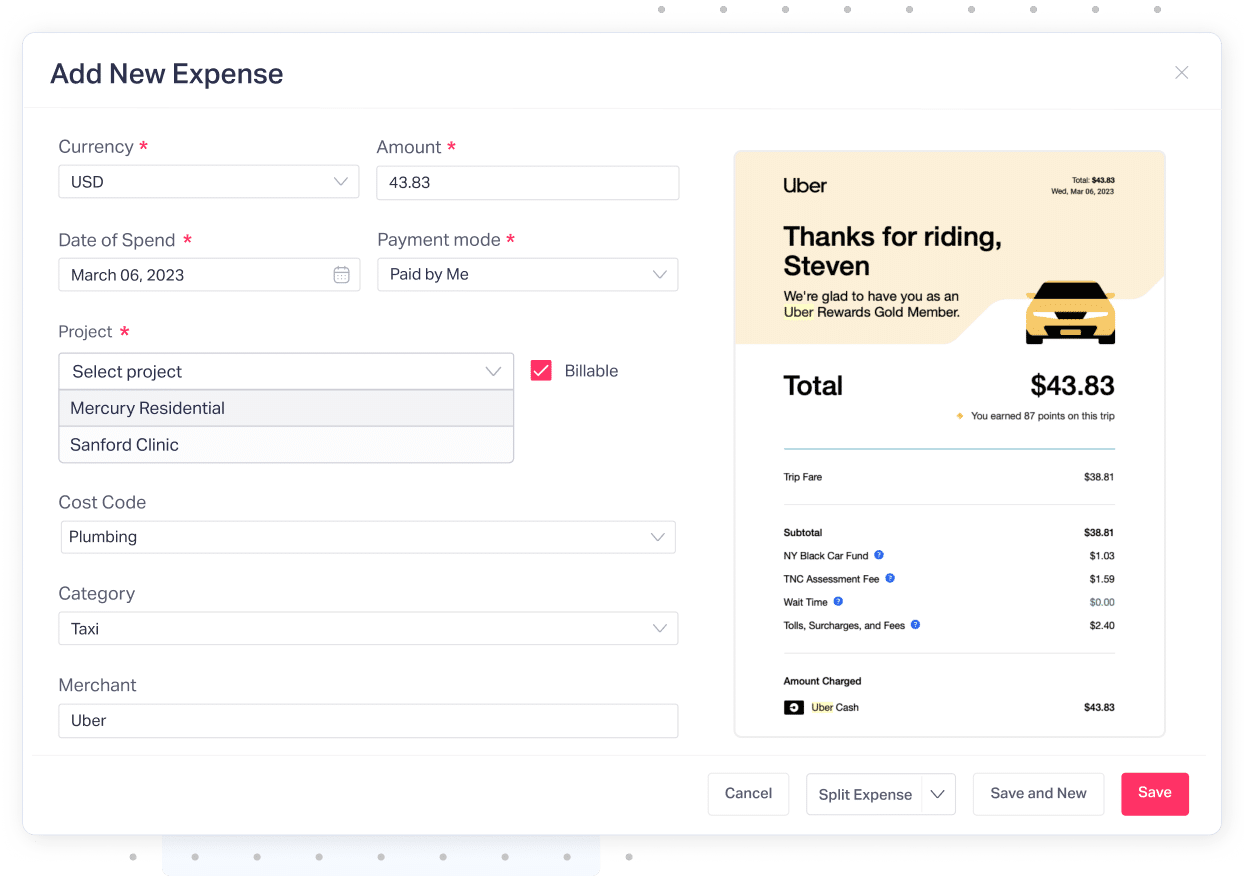
2. Improved efficiency
Automation can improve the efficiency of the manufacturer expense management process. Instead of depending on manual data entry and paper-based receipts, workers can upload digital tickets and use incorporated expense tracking tools.
At VEM Medicals, our automated system lets us review and approve expenses in a timely manner. We have access to expense reports online and can make decisions promptly. This eliminated delays caused by manual routing and approval processes. By extension, it reduces the time spent on administrative tasks, letting employees focus on core manufacturing activities.
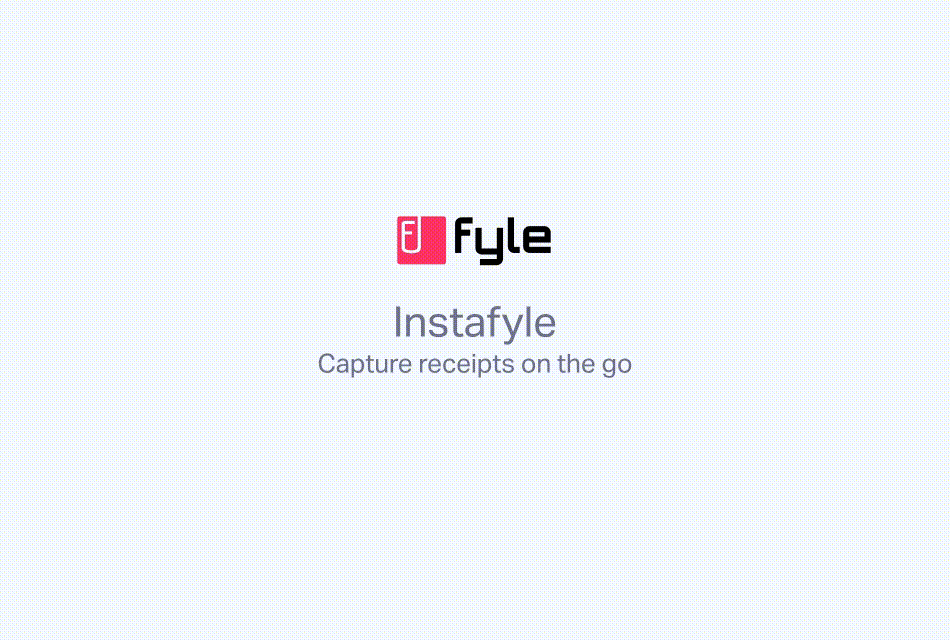
3. Compliance and Audit Trail
There are different rules, industry standards, and internal policies that manufacturers need to comply with. Automated expense management solutions help ensure compliance by enforcing expense policies and flagging potential breaches.
Each expense report is digitally recorded with details. These details include the date, time, location, expense category, and supporting receipts. This enables auditors to trace and verify expenses during internal or external audits easily.
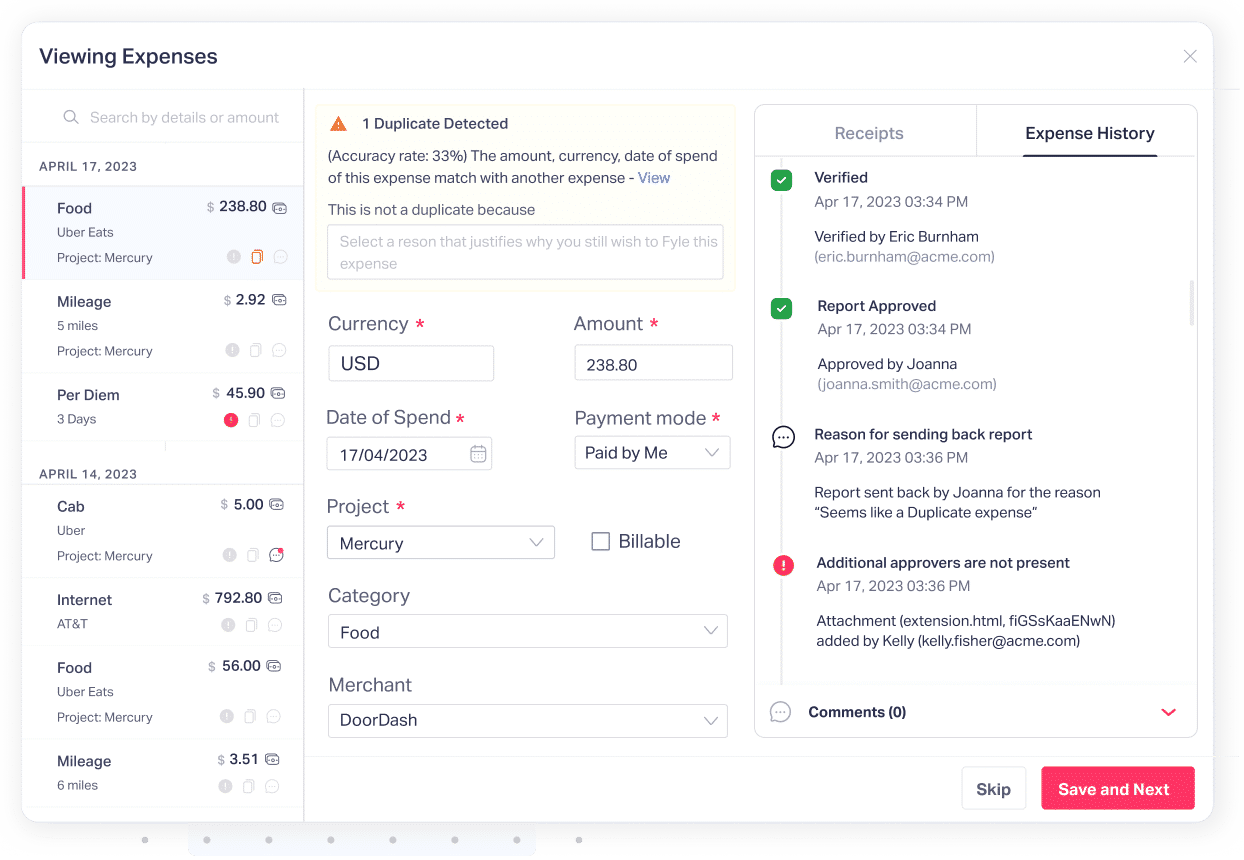
Also read:
4. Cost control and visibility
Automated expense management systems offer real-time visibility into manufacturing expenses. At VEM Medicals, employees easily submit their expense reports online using the automated solution. This streamlines the entire expense reporting process. It also eliminates the need for manual paperwork and reduces the chances of errors or missing information. Management can also scrutinize spending patterns to identify areas of overspending to implement measures to optimize expenses.
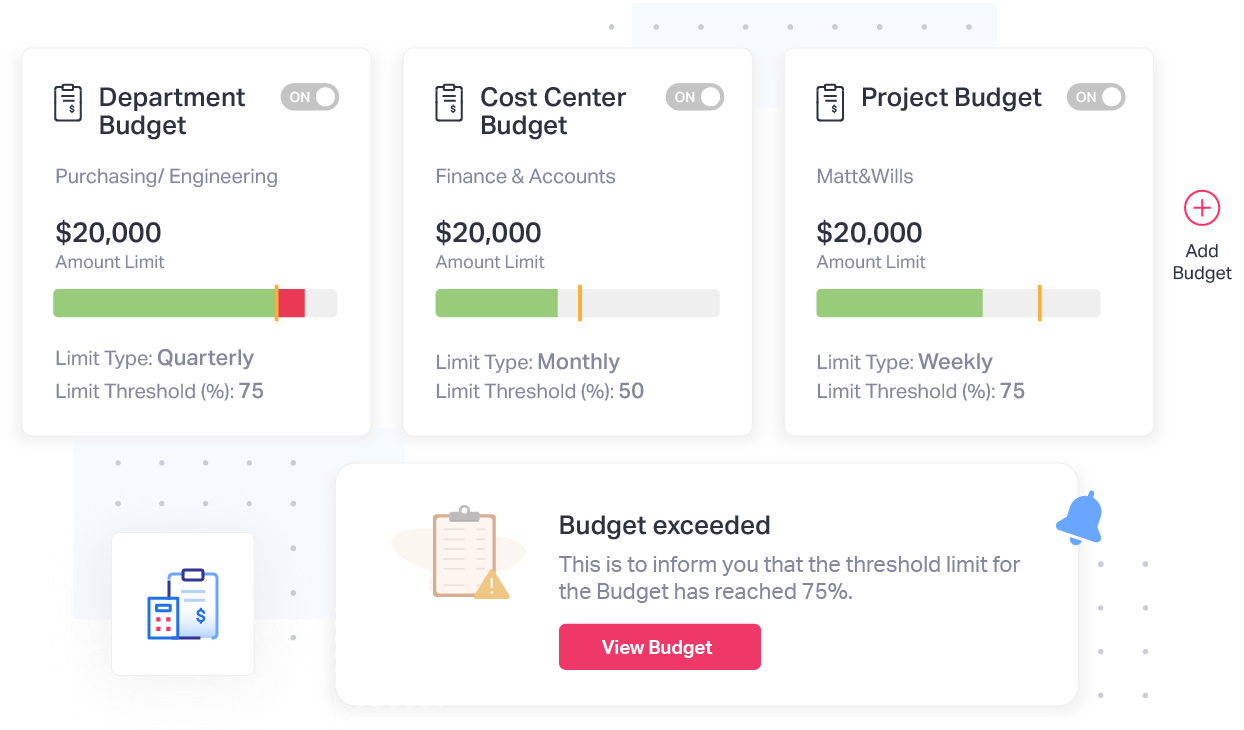
5. Integration with ERP systems
Most manufacturing companies use Enterprise Resource Planning (ERP) systems to manage their operations. An expense software that integrates seamlessly with your existing ERP system provides a total view of financial data. It also facilitates the automatic synchronization of expense data, eliminating manual data entry and errors. This ensures accurate financial reporting and improved data accuracy.
6. Budgeting and forecasting
Effective expense management for manufacturing comprises setting realistic budgets and forecasts for operations. This needs exploring historical data, market trends, production targets, and cost projections.
Automated systems simplify manufacturer expense management by allocating costs to specific projects, departments, or cost centers. This aids in budgeting and cost control by providing a clear breakdown of expenses across different areas of the organization. It also helps in identifying cost overruns and optimizing resource allocation.
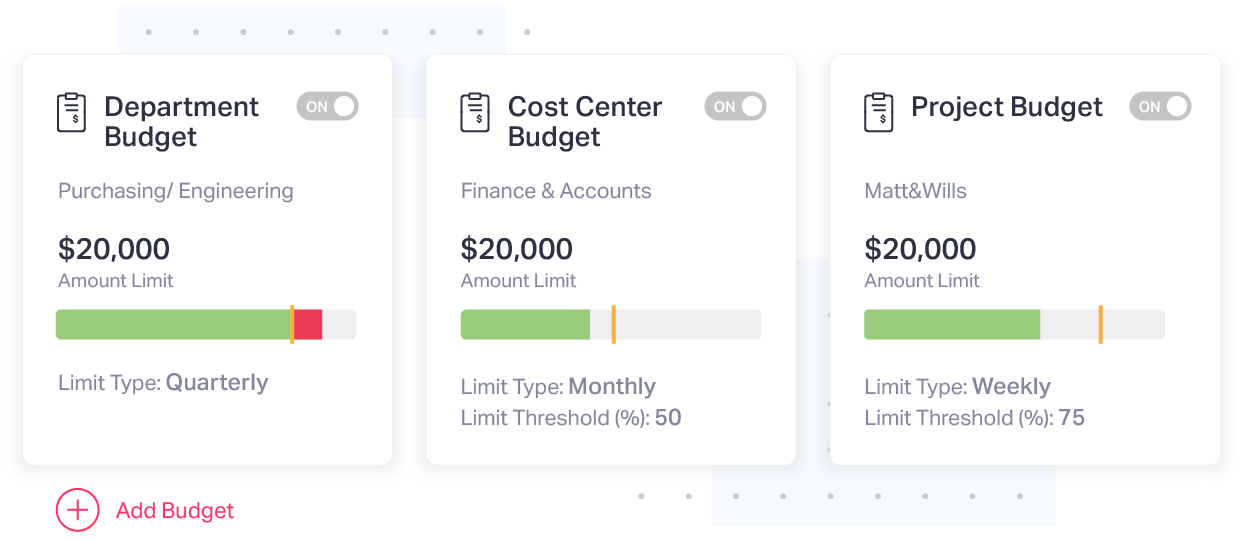
Also Read:
7. Expense approval workflows
Automated systems facilitate expense approval workflows by providing configurable rules and workflows. This ensures that expenses are reviewed and approved according to predefined policies and authorization levels. Managers can quickly review and support expenses, while employees can submit their expense claims digitally, simplifying the overall approval process.
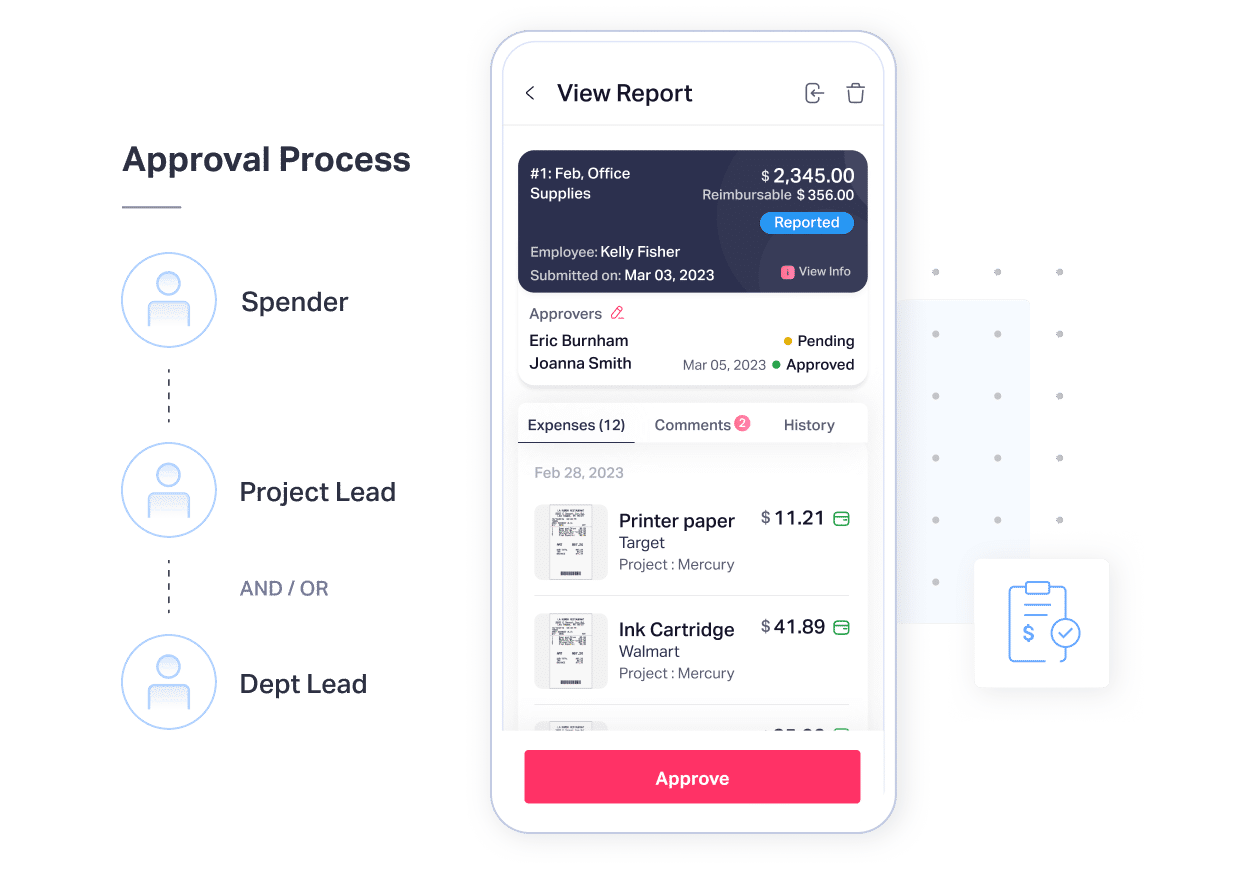
8. Compliance and risk management
Expense management software can seamlessly implement company policies and compliance regulations. Organizations can control expenses by defining spending limits, expense categories, and approval hierarchies. With these systems, they can ensure strict compliance with internal policies and external regulations.
Automated systems can also flag suspicious or out-of-policy expenses for further review and investigation. Managing risks linked with supply chain risks and changing economic conditions is a must for effective expense management for manufacturing.
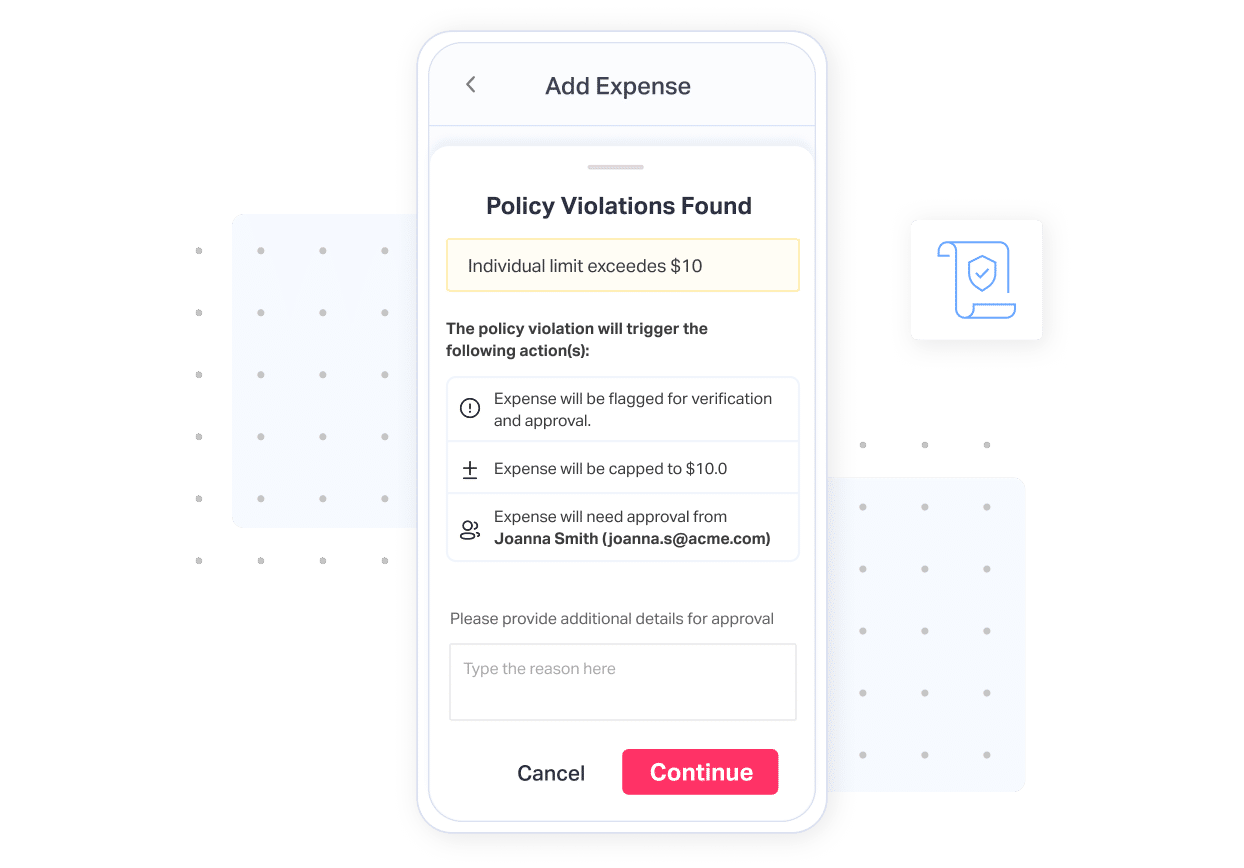
9. Enhanced employee experience
Manual expense management processes are time-consuming and frustrating for employees. By adopting an automated solution, employees can have a simplified process which will help expedite the expense reimbursement process. Employees can easily submit expense reports, track the status of their reimbursements, and receive timely payments. This enhances employee satisfaction and lessens the administrative burden on employees and finance teams.
Benefits of Effective Manufacturer Expense Management
- Improved cash flow: By carefully tracking and managing expenses, manufacturers can improve their cash flow and avoid financial difficulties. This is important for any business, but it is especially important for manufacturers, who often have large upfront costs associated with production.
- Increased efficiency: By streamlining manufacturing processes and eliminating waste, manufacturers can become more efficient and productive.
- Enhanced compliance with regulations: Manufacturers are subject to various regulations, including labor, environmental protection, and product safety. Manufacturers can reduce the risk of compliance violations by carefully tracking and managing their expenses.
- Improved decision-making: By accessing accurate and timely expense data, manufacturers can make better decisions about pricing, production, and other aspects of their business. This can lead to increased sales, improved efficiency, and a stronger bottom line.
- Stay ahead of competition: The manufacturing landscape is increasingly competitive, with manufacturers from all over the world vying for market share. By effectively managing their expenses, U.S. manufacturers can reduce costs and become more competitive.
- Improve profitability: Manufacturers can improve their bottom line by identifying and reducing unnecessary expenses. This is especially important in today's challenging economic climate.
In short, manufacturing expense management is essential for U.S. manufacturers who want to stay competitive, improve profitability, and comply with regulations. By effectively managing their expenses, manufacturers can make better decisions and position themselves for success in the global marketplace.
Examples of How U.S. Manufacturers Can Benefit From Manufacturing Expense Management
- A manufacturer of medical devices can use manufacturing expense management to identify areas where costs can be saved, such as by negotiating better deals with suppliers or streamlining production processes. This can help the manufacturer reduce costs and remain competitive globally.
- A furniture manufacturer can use manufacturing expense management to improve its cash flow by tracking its expenses carefully and ensuring that it is not overspending. This can help the manufacturer avoid financial difficulties and stay in business.
- A clothing manufacturer can use expense management software to track the cost of raw materials, labor, and other expenses involved in manufacturing a garment. This information can be used to set prices and make sure that the company is profitable.
- An electronic equipment manufacturer can use expense management software to track the cost of travel, meals, and lodging for employees who travel to trade shows or visit customers. This information can be used to control costs and make sure that the company is profitable.
By effectively managing their expenses, U.S. manufacturers can improve their competitiveness, profitability, cash flow, compliance, and decision-making. This can lead to increased sales, improved efficiency, and a stronger bottom line.
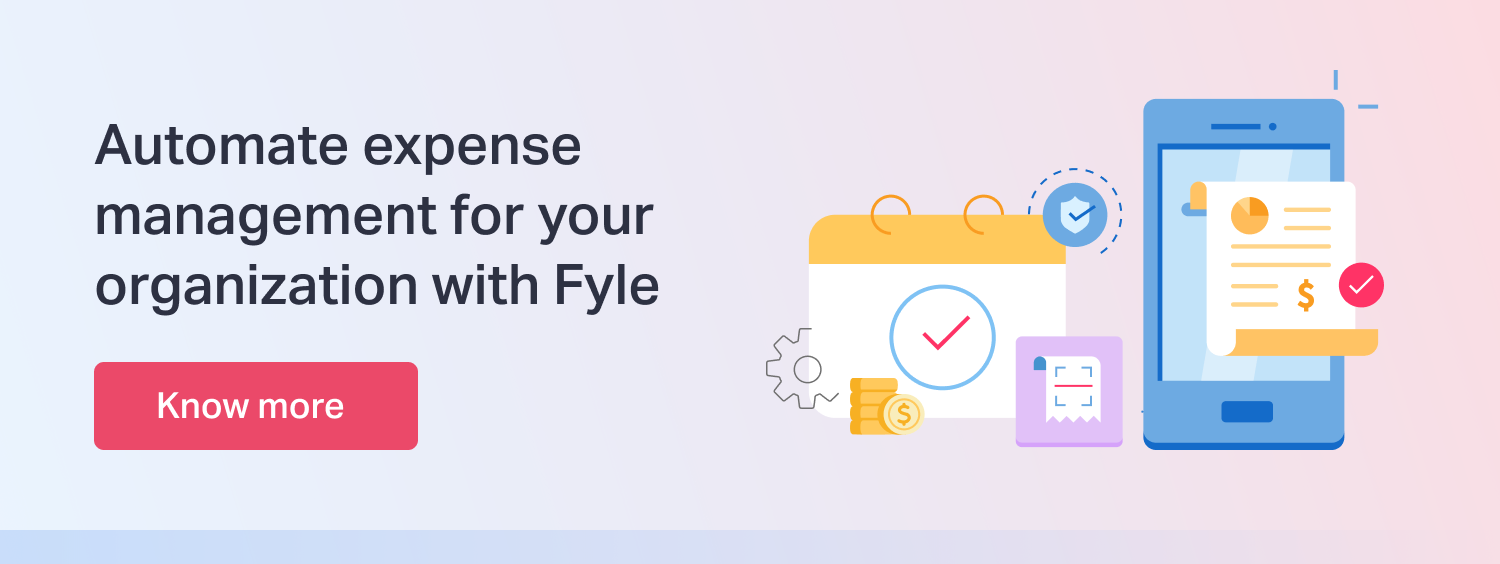
How to Implement an Automated Manufacturing Expense Management Solution
1. Assess your current expense management system: Understand how the company handles expense management. Identify problems, inefficiencies, and areas for improvement. Evaluate the specific requirements and challenges of managing expenses in a manufacturing setting.
2. Analyze available automated expense solutions: Use market research to identify expense management software and platforms that align with the company's needs. Choose solutions that provide features relevant to manufacturing expenses. This includes inventory tracking, project costing, or cost allocation to different departments.
3. Plan the implementation process: Create a detailed implementation plan with steps. Include the timelines and responsibilities for deploying the expense solution. Identify the data needed to migrate from the existing system and plan the necessary integrations with other software tools.
4. Configure the expense solution: Set up the expense management solution according to company requirements. Configure user roles, permissions, expense categories, approval workflows, and expense policies. Personalize the system to reflect the company's manufacturing-specific needs.
5. Test and train: Conduct extensive testing of the automated expense solution to ensure it works as expected. Train the workers on how to use the system efficiently. Teach them how to capture expenses, submit claims, and track approvals. Provide resources like user guides or training sessions to promote adoption.
6. Deploy and monitor: Gradually deploy the expense solution across the company. Track the system's performance, user feedback, and key metrics to identify any areas for improvement. Address any concerns promptly to ensure a successful rollout.
7. Constant improvement: Regularly review and enhance the expense management processes. Leverage the report and analytics abilities of the automated solution to gain insights into spending patterns. You can use it to identify cost-saving opportunities and make data-driven decisions. Also, seek user feedback and work on the system to improve its efficiency.
Conclusion
Effective expense management for manufacturing is essential for manufacturing companies to maintain financial stability, increase profitability, and achieve long-term success.
Automated expense management empowers manufacturers to capture, categorize, and track expenses in real-time, enabling timely decision-making and better cost control. It also reduces the risk of human error, ensuring accurate and reliable financial reporting.
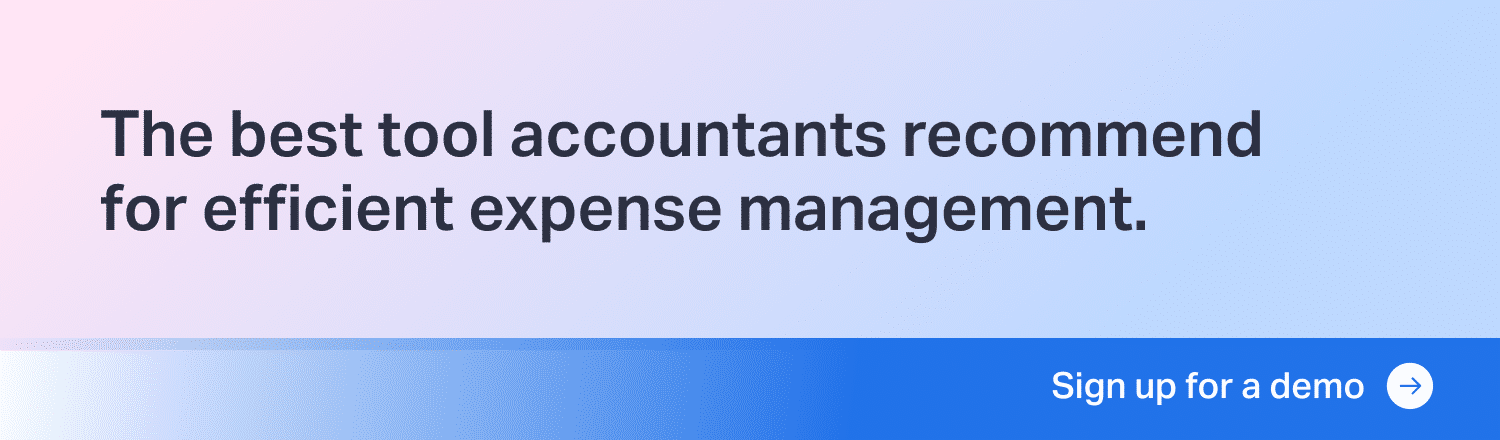
This blog has been edited by Shruti Kesavan.