Introduction
Construction projects are typically expensive, involving various costs such as labor, materials, and other miscellaneous expenses. Tracking all these expenses is difficult, so an effective method like job costing is essential. Job costing forecasts project expenses and helps you price your services to ensure profitability.
This guide covers everything you need to know about job costing—what it is, why it's important, how to implement it, examples, and much more.
What is Job Costing?
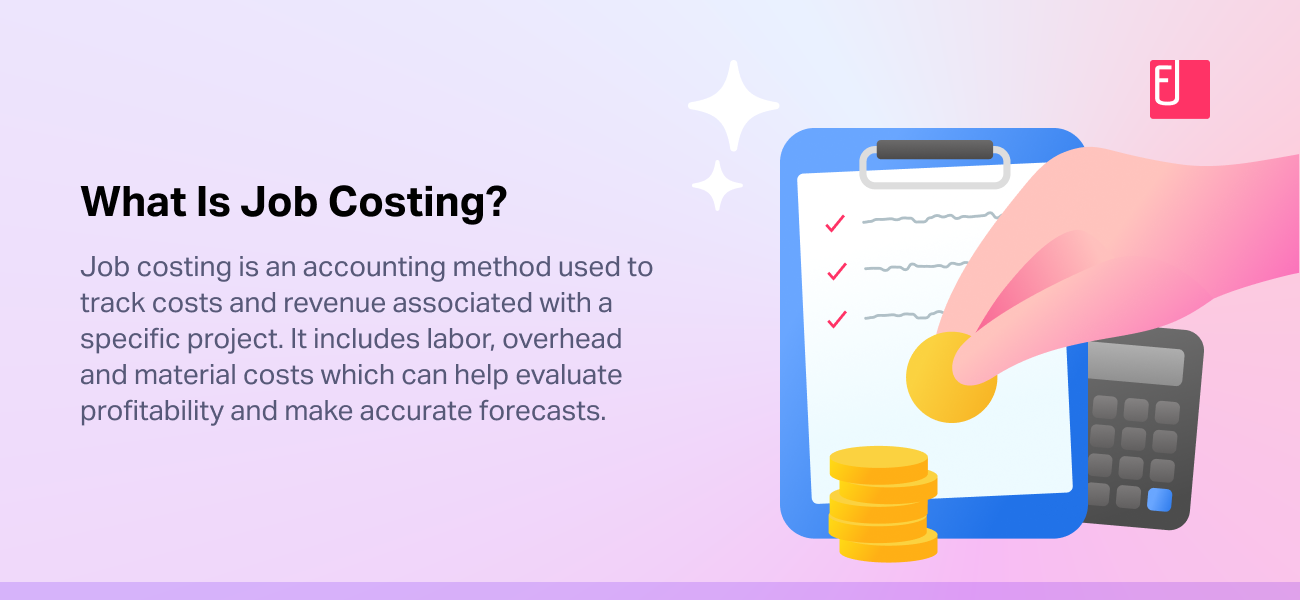
Job costing is an accounting method used to track expenses and revenue for specific projects. It meticulously accounts for every operating expense, including labor, materials, and overhead, which can be further broken down (we'll explore these in more depth below).
While job costing is most commonly associated with construction, it's also widely used in manufacturing, logistics, healthcare, and more industries. This method is popular because it relies on precise data rather than broad assumptions. A job costing system provides a clear picture of the expenses and profits that went into each project and offers insights into areas where you can reduce costs to enhance profitability for future projects.
Why is Job Costing Important?
When done correctly, job costing can greatly benefit your business. It enables you to balance revenue and costs for specific projects by offering a detailed overview of every expense and utilizing historical data for informed decision-making. Additionally, having access to detailed information can reduce unexpected expenses, improve profit margins, and strengthen client relationships.
Job order costing also supports finance and accounting teams during tax season and provides a clear understanding of how much the company can financially handle.
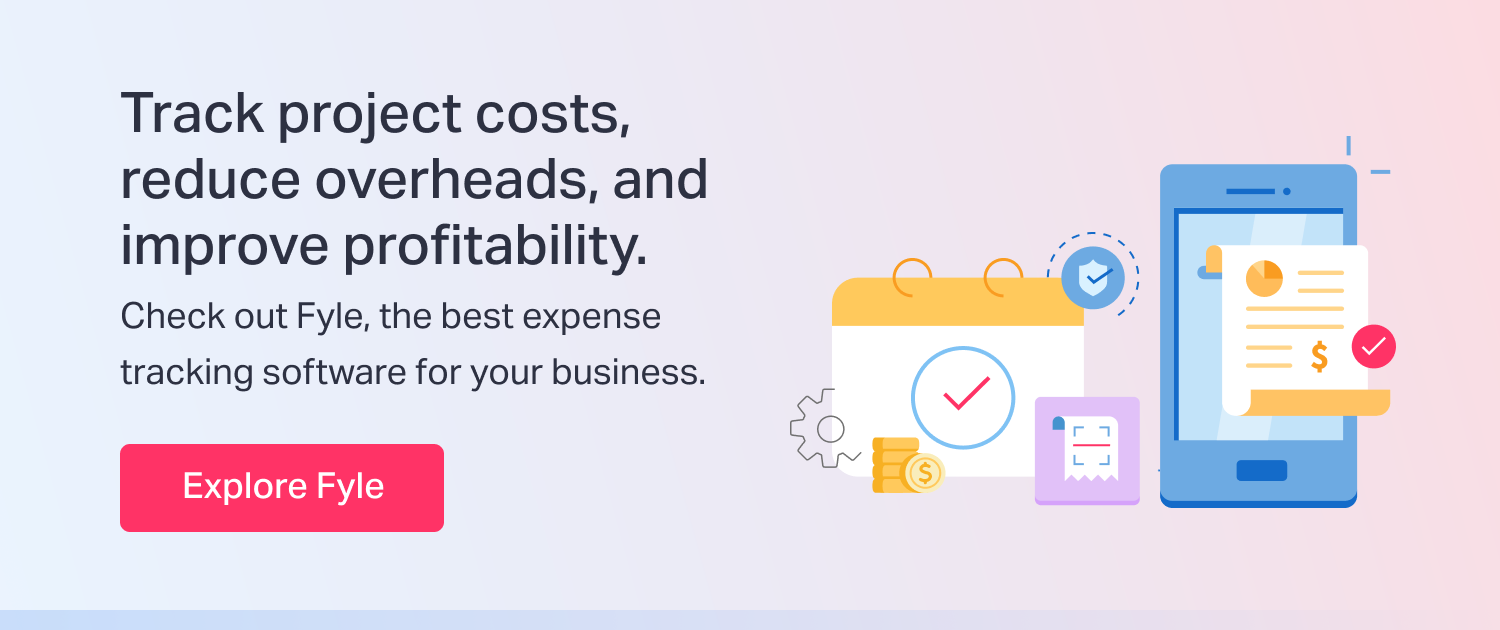
What is a Costing Sheet?
Before we learn how to calculate job costing, let’s look at one of the tools that aid in job costing, called a costing sheet.
A costing sheet is a comprehensive list of all expenditures for a project. It leverages unit pricing and uses historical data to facilitate comparisons. This tool is particularly effective for expensive or complex projects, providing a detailed breakdown of costs at a unit level.
Benefits of using a costing sheet include:
- Displaying both the overall project cost and unit costs.
- Utilizing historical prices to aid in accurate forecasting.
- Assisting in the development of pricing strategies and benchmarking incurred costs.
How to Calculate Job Costing?
Job costing involves adding a specific project's labor, material, and overhead costs. Let's explore how to calculate each component accurately:
Calculating Labor Costs
Labor costs are a key component when calculating job costing. These costs encompass the wages paid to workers and staff involved in a specific project. To calculate this, you typically multiply the daily rate, the number of workers, and the estimated duration of the project.
It's important to remember that if subcontractors are hired for specialized tasks beyond your company's expertise, their costs should be included. This ensures that your labor cost calculations are accurate and comprehensive.
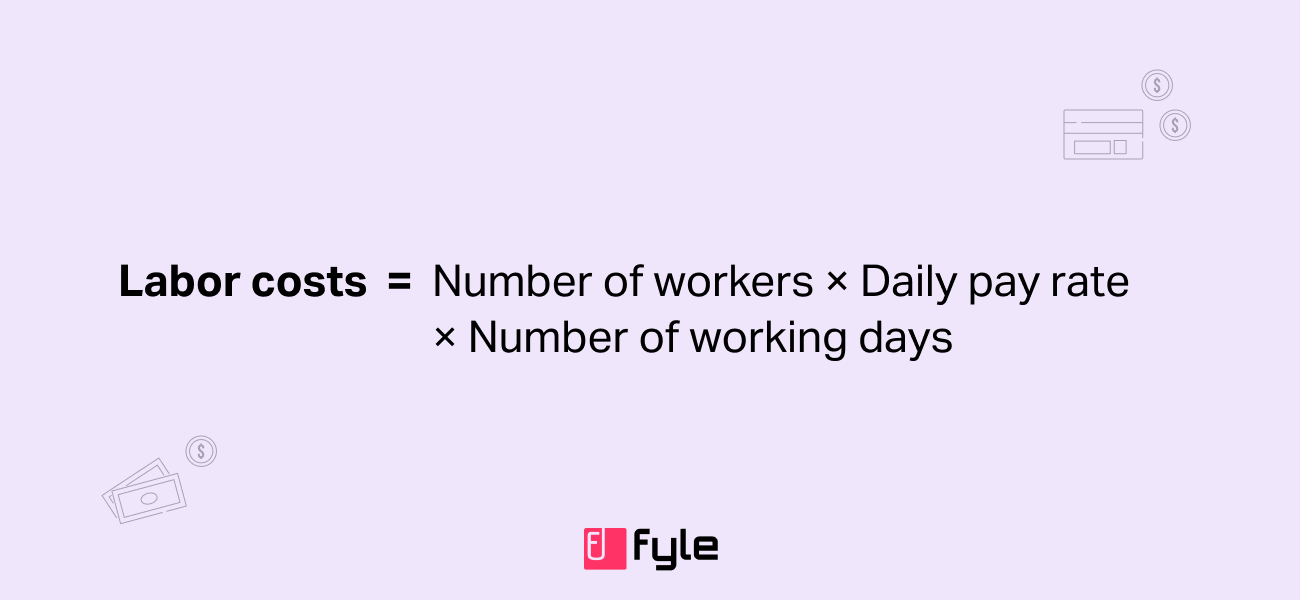
Calculating Material Costs
To calculate material costs, you add all the direct and indirect expenses associated with completing a job. Direct costs include the materials used in the final product, such as concrete, wood, wiring, and screws. Indirect costs can be items like machinery, equipment, and safety gear.
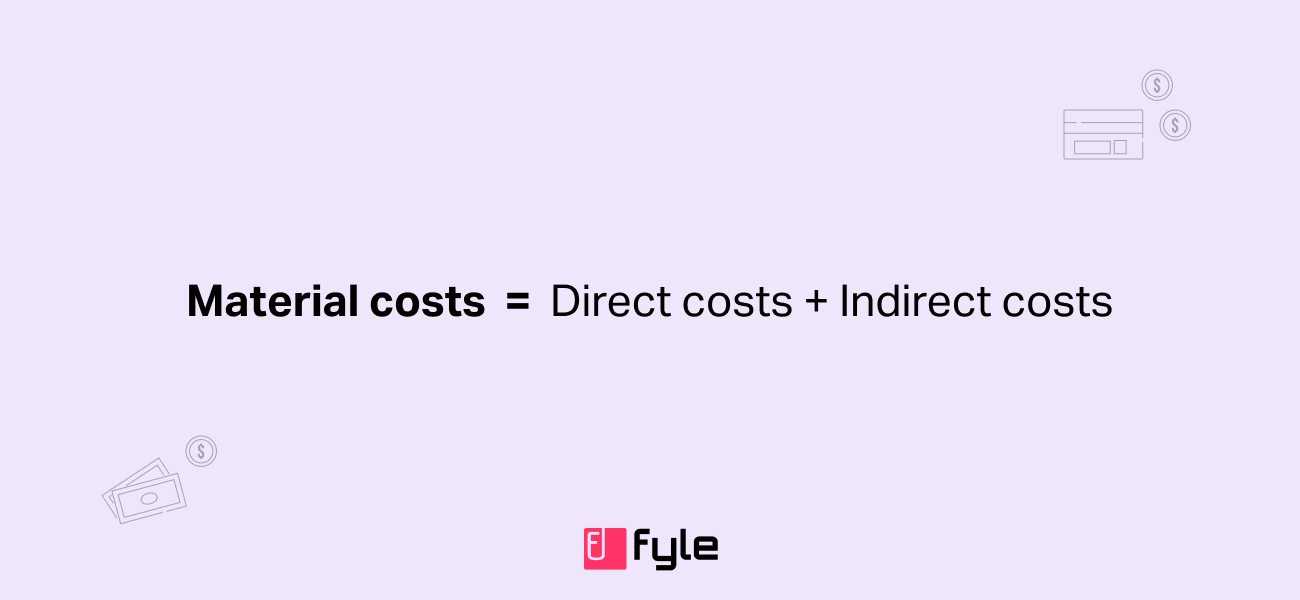
Calculating Overhead Costs
Overhead costs are often the most challenging aspect of job costing. These include estimated daily expenses necessary to complete a project, such as rent, depreciation, machine running costs, utilities, and more. Due to the complexity of accurately estimating these costs, businesses typically apply a standard overhead fee to each project.
Once you have all the above costs, calculating job order costing is easy. To simplify and streamline the calculation process, you can use a job costing software.
Job Costing Formula
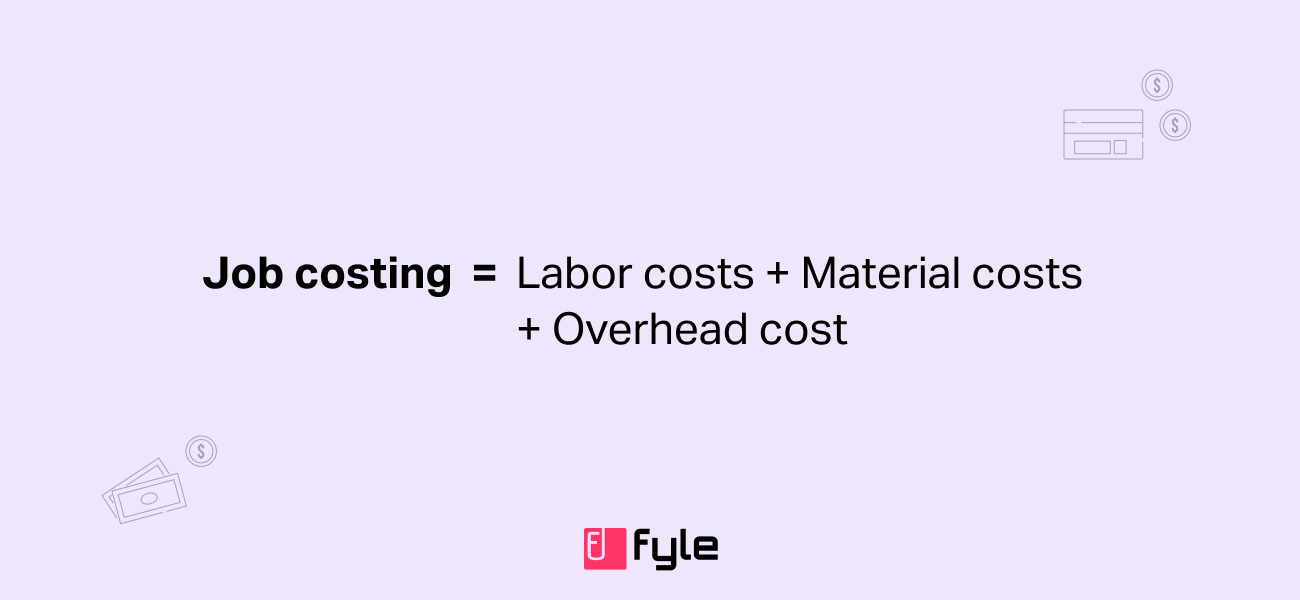
Example of Job Costing
Let's consider a construction project to build a small residential house. Here's a breakdown of the costs involved:
Labor Costs
- Project manager: $5,000
- Site supervisor: $4,000
- Skilled laborers: $25,000
Total Labor Costs: $34,000
Material Costs
- Concrete and cement: $8,000
- Bricks and blocks: $6,000
- Steel and rebar: $10,000
- Lumbar: $5,000
- Other supplies: $8,000
Total Material Costs: $37,000
Overhead Costs
- Rent for equipment: $2,000
- Depreciation on tools and machinery: $1,500
- Utilities: $1,000
- Miscellaneous (permits, admin costs): $1,500
Total Overhead Costs: $6,000
Total Job Cost = Labor + Material + Overhead = $77,000
Your total job cost for your clients’ project will be $77,000.
When to Use Job Costing?
Job costing is a beneficial practice for any industry, offering a detailed view of all potential project costs. This insight enables businesses to better anticipate expenses and prepare accordingly.
In the construction industry, for example, numerous workers and supplies are involved in each project, making detecting overspending challenging. Tracking construction expenses on a project basis allows managers to create more accurate forecasts and identify unexpected costs that could impact profits.
Similarly, job costing is invaluable in the manufacturing industry. A comprehensive breakdown of labor, material, and overhead costs using a job costing software helps businesses set prices effectively and measure profitability. Additionally, job costing enables more accurate budget preparation and provides a clearer view of operating expenses.
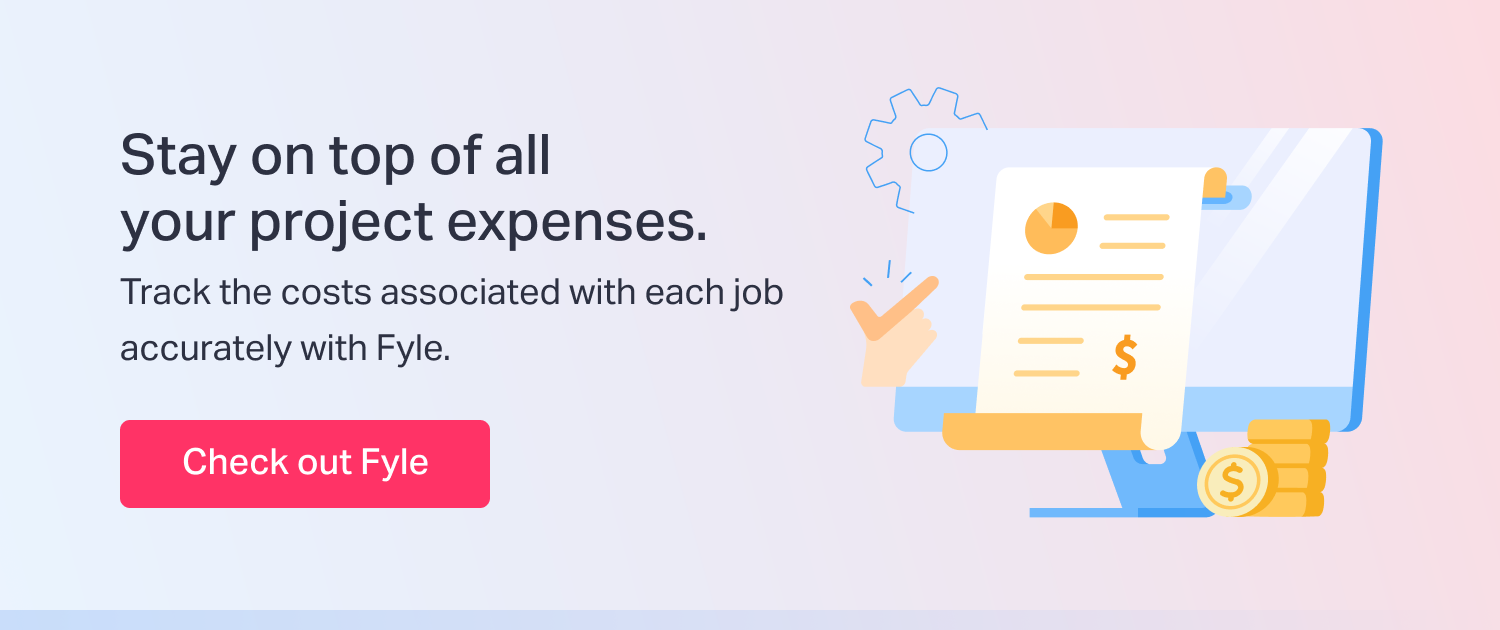
What are the Benefits of Job Costing?
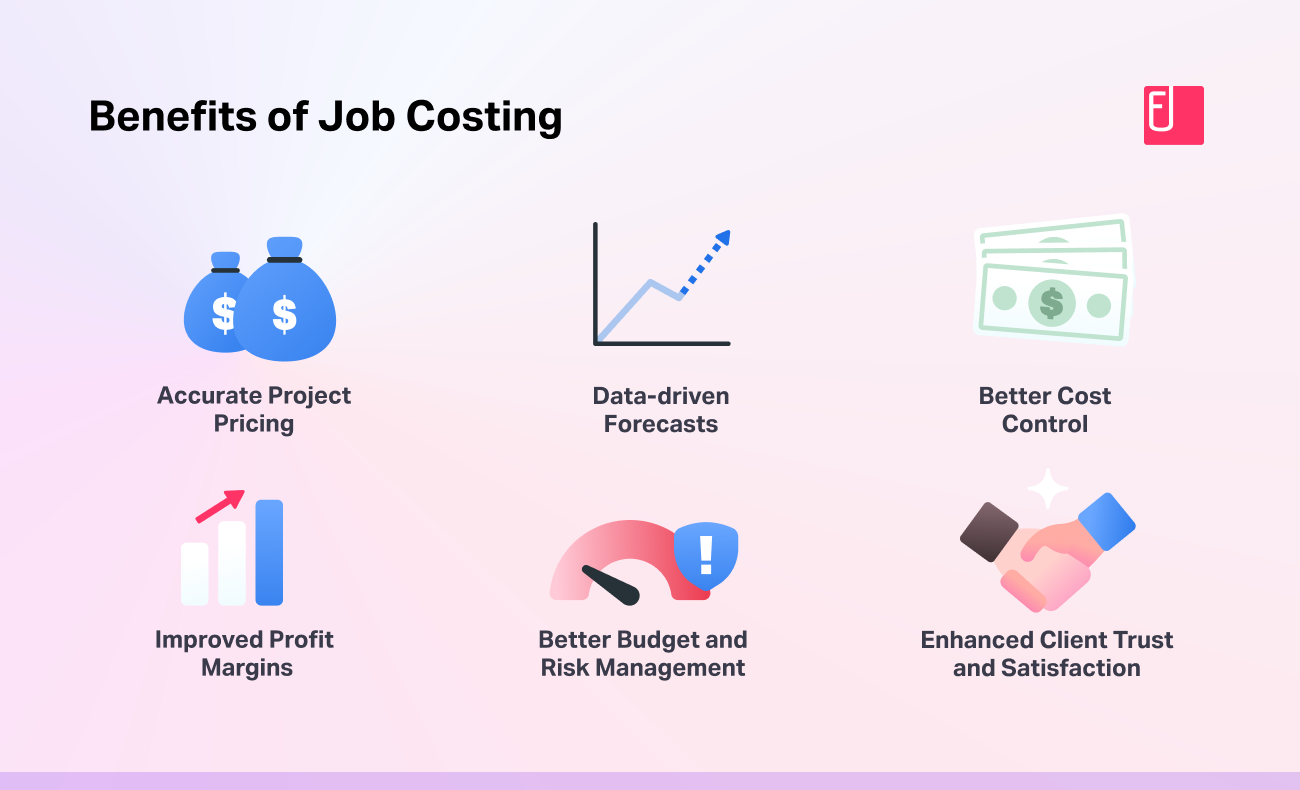
Implementing a job costing system is highly beneficial for businesses. By breaking down large-scale and complex projects to a unit level, job costing simplifies management, enhances profit recognition, and helps in ensuring the financial sustainability of the company.
Accurate project pricing
Since job costing calculates expenses at a unit level, it avoids underestimations and ensures that all costs are covered with accurate and competitive pricing.
Data-driven forecasts
Job costing provides reliable forecasts as it utilizes detailed historical data as well as current project information. This enables better planning and resource allocation for present and future projects.
Better cost control
You can identify where money is being spent and identify areas where costs can be reduced. This results in more efficient resource use and minimizes unnecessary expenditures.
Improved profit margins
With accurate cost tracking and better pricing strategies, job costing ensures that products and projects are profitable. It helps identify which projects you should focus on and where you might be wasting money and effort.
Also Read:
Better budget and risk management
Job costing provides a clear view of all the direct and indirect costs and how they affect the budget. It also gives you a better idea of the potential risks, allowing for proactive management. This leads to fewer financial surprises and better handling of unforeseen issues.
Enhanced client trust and satisfaction
Job costing boosts client confidence by delivering projects on time and under budget. Being transparent with your costing builds trust and leads to higher client satisfaction and repeat business.
Who Uses Job Costing?
Job costing is a versatile accounting method that can be utilized by businesses across various industries. Although it is most commonly associated with construction, many other sectors can also benefit from job order costing.
Here are a few examples:
Healthcare: Healthcare businesses face numerous expenses, including salaries for doctors and medical staff, lab costs, medical equipment, and cleaning supplies. Job costing helps manage these expenses and enables more accurate forecasting.
Marketing & Advertising Firms: These businesses charge clients based on the resources used for a project. By calculating rent, supplies, software, and other costs, they can better determine project pricing, reducing the likelihood of client pushback.
Logistics & Retail: Operating a warehouse demands meticulous planning and execution. Regularly monitoring and adjusting costs such as warehouse rent, wages, and infrastructure is essential for minimizing issues and maximizing profitability.
Conclusion
Job costing is a powerful tool that empowers businesses to gain control over their finances and ensure project profitability. By providing a detailed breakdown of all expenses at a unit level, job costing enables businesses to make data-driven decisions, better allocate resources, and streamline project management.
To simplify and improve your job costing calculations, consider using an expense tracking software like Fyle or an accounting software with job costing. Fyle can integrate with your accounting software and efficiently track all project receipts and expenses on the go, providing accurate, updated information to further enhance your projects' profitability and success.
FAQs
What is process costing?
Process costing is an accounting method used to track the cost of production for mass-produced items. The cost is calculated on the basis of the process and not on the basis of the job. For example, if you're a cookie factory making thousands of identical cookies, instead of tracking the cost of each cookie, you track costs for each step, like mixing, baking, and packaging. Then, divide the total cost by the number of cookies to find the average cost per cookie. This helps manage expenses and set prices.
What's the difference between job costing and process costing?
The key difference is that job costing tracks expenses for a project, like building a house, whereas process costing tracks expenses for each stage of production for mass-produced items. In process costing, costs are recorded for each stage of production and then averaged over the total number of products to determine the cost per unit.
Why use job costing instead of process costing?
While deciding job costing vs process costing, If you need to track costs for individual projects with pinpoint accuracy, choose job costing. For determining average costs of mass-produced products, use process costing.
What are the disadvantages of job costing?
- Job costing is time-consuming and highly manual - it requires meticulous tracking of expenses for each project.
- It can be challenging to calculate unexpected costs, which could lead to inaccuracies in estimations and pricing.
- It may not be well suited for businesses that engage in mass production or standardized procedures.
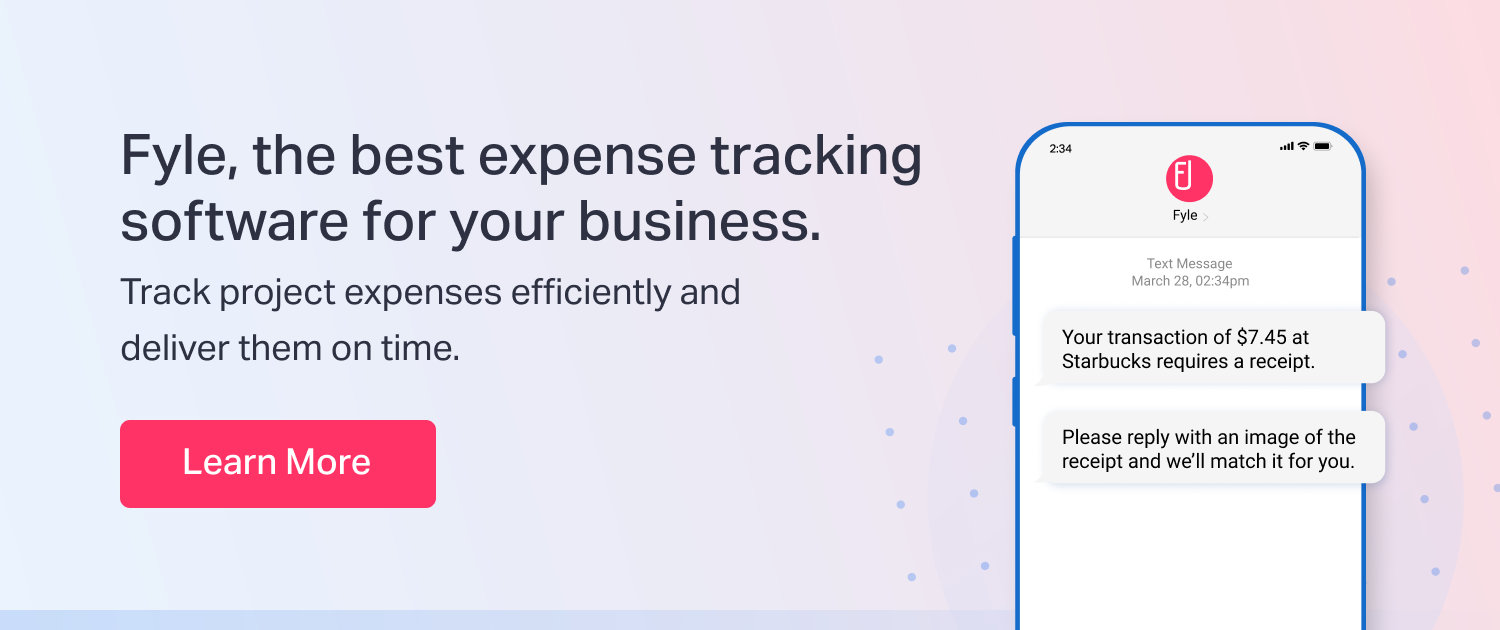